توسعه و روند فناوری ذوب القایی خلاء
با توسعه سریع فناوری مدرن صنعتی، نیازهای مردم برای استفاده از قطعات مکانیکی بیشتر و بیشتر می شود و محیط استفاده شدیدتر، نیازهای بالاتری را برای مقاومت در برابر دمای بالا، مقاومت در برابر سایش، مقاومت در برابر خستگی و سایر خواص مواد فلزی مطرح می کند. .
برای برخی از فلزات یا مواد آلیاژی خاص، چه آزمایش تحقیق و توسعه در مراحل اولیه باشد و چه تولید انبوه در مراحل بعدی، تحقیق یا به دست آوردن مواد آلیاژی فلزی با کارایی بالا نیاز به پشتیبانی تجهیزات ذوب فلز، تجهیزات عملیات حرارتی سطح و غیره دارد. در بسیاری از روشهای ویژه گرمایش یا ذوب، از فناوری گرمایش القایی برای ذوب و آمادهسازی مواد فلزی یا پخت و عملیات حرارتی مواد در فرآیند خاصی استفاده میشود که نقش حیاتی داشته است.
این مقاله به معرفی فرآیند توسعه فناوری ذوب القایی خلاء و کاربرد فناوری ذوب القایی در مناسبتهای مختلف میپردازد. با توجه به ساختار انواع مختلف کوره های القایی خلاء، مزایا و معایب آنها را مقایسه کنید. به دنبال جهت توسعه آینده کوره های القایی خلاء، روند توسعه آن را توضیح می دهد. توسعه و پیشرفت کورههای القایی خلاء عمدتاً در بهبود تدریجی ساختار کلی تجهیزات، روند آشکارتر مدولارسازی و سیستم کنترل هوشمندتر منعکس میشود.
1. تکنولوژی ذوب القایی خلاء
1.1 اصل
__kindeditor_temp_url__فناوری گرمایش القایی معمولاً به فناوری اطلاق می شود که از اصل القای الکترومغناطیسی برای به دست آوردن جریان القایی برای مواد با حساسیت مغناطیسی بهتر برای دستیابی به هدف گرمایش در شرایط خلاء استفاده می کند. جریان الکتریکی از سیم پیچ الکترومغناطیسی اطراف ماده فلزی با فرکانس مشخصی عبور می کند. جریان الکتریکی متغیر یک میدان مغناطیسی القایی ایجاد می کند که باعث ایجاد جریان القایی در فلز می شود و مقدار زیادی گرما برای گرم کردن مواد ایجاد می کند. هنگامی که گرما نسبتاً کم است، می توان از آن در عملیات حرارتی القایی خلاء و سایر فرآیندها استفاده کرد. هنگامی که حرارت زیاد است، حرارت تولید شده به اندازه ای است که فلز را ذوب کرده و برای تهیه مواد فلزی یا آلیاژی استفاده شود.
1.2 ، برنامه
1.2.1 ذوب القایی خلاء
فن آوری ذوب القایی خلاء در حال حاضر کارآمدترین، سریع ترین، کم مصرف ترین، صرفه جویی در انرژی و سازگار با محیط زیست فناوری گرمایش القایی برای گرم کردن مواد فلزی است. این فناوری عمدتاً در کوره های ذوب القایی و سایر تجهیزات اجرا می شود و کاربردهای گسترده ای دارد. مواد خام فلزی جامد در یک بوته پیچیده شده توسط یک سیم پیچ قرار می گیرند. هنگامی که جریان از سیم پیچ القایی عبور می کند، یک نیروی الکتروموتور القایی ایجاد می شود و یک جریان گردابی در داخل بار فلزی ایجاد می شود. وقتی گرمای فعلی بیشتر از سرعت اتلاف گرمای بار فلز باشد، گرما بیشتر و بیشتر جمع میشود وقتی به یک سطح معین میرسد، فلز از حالت جامد به حالت مایع ذوب میشود تا به هدف ذوب فلزات برسد. در این فرآیند، از آنجایی که کل فرآیند در محیط خلاء انجام می شود، حذف ناخالصی های گاز داخل فلز مفید است و مواد آلیاژی فلزی به دست آمده خالص تر است. در عین حال، در طول فرآیند ذوب، از طریق کنترل محیط خلاء و گرمایش القایی، می توان دمای ذوب را تنظیم کرد و فلز آلیاژی را می توان به موقع تکمیل کرد تا به هدف پالایش دست یافت. در طول فرآیند ذوب، با توجه به ویژگی های فن آوری ذوب القایی، مواد فلزی مایع داخل بوته را می توان به طور خودکار به دلیل تعامل نیروی الکترومغناطیسی به هم زد تا ترکیب یکنواخت تر شود. این نیز یک مزیت عمده فناوری ذوب القایی است.
در مقایسه با ذوب سنتی، ذوب القایی خلاء به دلیل صرفه جویی در انرژی، حفاظت از محیط زیست، محیط کار خوب برای کارگران و شدت کار کم مزایای زیادی دارد. با استفاده از فناوری ذوب القایی، مواد آلیاژی نهایی ناخالصی کمتری دارند و نسبت آلیاژ اضافه شده مناسبتر است که میتواند نیازهای فرآیند را برای خواص مواد برآورده کند.
فناوری ذوب القایی خلاء در مقیاس وسیعی از کوره های القایی چند کیلوگرمی برای تحقیقات تجربی گرفته تا کوره های القایی در مقیاس بزرگ با ظرفیت ده ها تن برای تولید واقعی استفاده شده است. به دلیل فناوری عملیات ساده آن، کنترل فرآیند ذوب آسان است و دمای ذوب سریع است. ، فلز ذوب شده دارای مزایای ترکیب یکنواخت است و چشم انداز کاربرد زیادی دارد و در سال های اخیر به سرعت توسعه یافته است.
1.2.2، تف جوشی القایی خلاء
تف جوشی خلاء به تف جوشی فلز، آلیاژ یا پودر ترکیب فلزی به محصولات فلزی و قطعات فلزی در دمای کمتر از نقطه ذوب در محیطی با درجه خلاء (10-10-3Pa) اطلاق می شود. تف جوشی در شرایط خلاء، هیچ واکنشی بین فلز و گاز وجود ندارد و هیچ تاثیری از گاز جذب شده وجود ندارد. نه تنها اثر متراکم شدن خوب است، بلکه می تواند نقش تصفیه و کاهش را نیز ایفا کند، دمای تف جوشی را کاهش می دهد، و نسبت تف جوشی در دمای اتاق را می توان تا 100 ℃ ~ 150 ℃ کاهش داد، در مصرف انرژی صرفه جویی کرد، باعث بهبود عمر کوره پخت و به دست آوردن محصولات با کیفیت بالا.
برای برخی از مواد، لازم است پیوند بین ذرات از طریق انتقال اتم ها از طریق گرمایش محقق شود و فناوری تف جوشی القایی نقش گرمایشی را در این فرآیند ایفا می کند. مزیت تف جوشی القایی خلاء این است که به کاهش مواد مضر (بخار آب، اکسیژن، نیتروژن و سایر ناخالصی ها) در اتمسفر در شرایط خلاء کمک می کند و از یک سری واکنش ها مانند کربن زدایی، نیترید کردن، کربورسازی، کاهش و اکسیداسیون جلوگیری می کند. . در طی فرآیند، مقدار گاز در منافذ کاهش می یابد و واکنش شیمیایی مولکول های گاز کاهش می یابد. در عین حال، فیلم اکسید روی سطح ماده قبل از ظاهر شدن مواد در فاز مایع برداشته می شود، به طوری که در هنگام ذوب شدن و چسباندن مواد، چسبندگی متراکم تری پیدا می کند و مقاومت به سایش آن بهبود می یابد. استحکام - قدرت. علاوه بر این، تف جوشی القایی خلاء نیز تأثیر خاصی در کاهش هزینه های محصول دارد.
از آنجایی که محتوای گاز در محیط خلاء نسبتاً کم است، جابجایی و هدایت گرما را می توان نادیده گرفت. گرما عمدتاً به صورت تشعشع از جزء گرمایشی به سطح ماده منتقل می شود. انتخاب بر اساس دمای پخت خاص و خواص فیزیکی و شیمیایی مواد است. اجزای گرمایشی مناسب نیز بسیار مهم هستند. در مقایسه با گرمایش مقاومت در خلاء، تف جوشی القایی از گرمایش توان فرکانس متوسط استفاده می کند، که از مشکل عایق حرارت بالا کوره های خلاء که از گرمایش مقاومتی تا حد معینی استفاده می کنند جلوگیری می کند.
در حال حاضر فناوری پخت القایی عمدتاً در زمینه های فولاد و متالورژی استفاده می شود. علاوه بر این، بر روی مواد سرامیکی خاص، تف جوشی القایی پیوند ذرات جامد را افزایش میدهد، به رشد دانههای کریستال کمک میکند، فضاهای خالی را فشرده میکند، و سپس چگالی را افزایش میدهد تا اجسام متخلخل چند کریستالی متراکم ایجاد شود. فناوری تف جوشی القایی نیز به طور گسترده در تحقیقات مواد جدید مورد استفاده قرار می گیرد.
1.2.3، عملیات حرارتی القایی خلاء
در حال حاضر، باید فناوری عملیات حرارتی القایی بیشتری وجود داشته باشد که عمدتاً در فناوری سخت شدن القایی متمرکز شده است. قطعه کار را داخل سلف (کویل) قرار دهید، هنگامی که یک جریان متناوب با فرکانس مشخص از سلف عبور می کند، یک میدان مغناطیسی متناوب در اطراف آن ایجاد می شود. القای الکترومغناطیسی میدان مغناطیسی متناوب باعث ایجاد جریان گردابی بسته در قطعه کار می شود. به دلیل اثر پوستی، یعنی توزیع جریان القایی روی سطح مقطع قطعه کار بسیار ناهموار است، چگالی جریان در سطح قطعه کار بسیار زیاد است و به تدریج به سمت داخل کاهش می یابد.
انرژی الکتریکی جریان با چگالی بالا روی سطح قطعه کار به انرژی گرمایی تبدیل می شود که باعث افزایش دمای سطح می شود، یعنی گرم شدن سطح را محقق می کند. هرچه فرکانس جریان بیشتر باشد، اختلاف چگالی جریان بین سطح و داخل قطعه کار بیشتر می شود و لایه گرمایش نازکتر می شود. پس از اینکه دمای لایه گرمایش از دمای نقطه بحرانی فولاد فراتر رفت، برای دستیابی به خاموش شدن سطح به سرعت سرد می شود. از اصل گرمایش القایی می توان فهمید که عمق نفوذ جریان را می توان با تنظیم فرکانس جریان از طریق سیم پیچ القایی به طور مناسب تغییر داد. عمق قابل تنظیم نیز مزیت اصلی عملیات حرارتی القایی است. با این حال، تکنولوژی سخت کاری القایی به دلیل سازگاری ضعیف برای قطعات کار مکانیکی پیچیده مناسب نیست. اگرچه لایه سطحی قطعه کار خاموش شده دارای تنش داخلی فشاری بیشتری است، مقاومت در برابر شکست خستگی بالاتر است. اما فقط برای تولید خط مونتاژ قطعات کار ساده مناسب است.
در حال حاضر، استفاده از فن آوری سخت شدن القایی عمدتا در خاموش کردن سطح میل لنگ استفاده می شودمحوراس و بادامکمحوردر صنعت خودروسازی اگرچه این قطعات ساختار ساده ای دارند، اما محیط کار خشن است، دارای درجه خاصی از مقاومت در برابر سایش، مقاومت خمشی و مقاومت در برابر عملکرد قطعات هستند. الزامات خستگی، از طریق سخت شدن القایی برای بهبود مقاومت در برابر سایش و مقاومت در برابر خستگی نیز معقول ترین روش برای برآورده کردن الزامات عملکرد است. به طور گسترده ای در درمان سطح برخی از قطعات در صنعت خودروسازی
2. تجهیزات ذوب القایی خلاء
تجهیزات ذوب القایی خلاء از فناوری ذوب القایی برای تحقق این اصل در استفاده واقعی از طریق تطبیق ساختار مکانیکی استفاده می کنند. این تجهیزات معمولاً از اصل القای الکترومغناطیسی برای قرار دادن سیم پیچ القایی و مواد در یک حفره بسته استفاده می کنند و گاز موجود در ظرف را از طریق یک سیستم پمپاژ خلاء استخراج می کنند و سپس از منبع تغذیه برای عبور جریان از سیم پیچ القایی استفاده می کنند. یک نیروی الکتروموتور القایی ایجاد می کند و در داخل ماده قرار می گیرد یک گرداب تشکیل می شود و زمانی که تولید گرما به حد معینی می رسد، ماده شروع به ذوب شدن می کند. در طول فرآیند ذوب، یک سری عملیات مانند کنترل توان، اندازهگیری دما، اندازهگیری خلاء و تغذیه تکمیلی از طریق سایر اجزای نگهدارنده روی تجهیزات انجام میشود و در نهایت فلز مایع از طریق وارونگی بوته به داخل قالب ریخته میشود تا شکل شمش فلزی بو کنید. ساختار اصلی تجهیزات ذوب القایی خلاء شامل قسمت های زیر است:
علاوه بر اجزای فوق، کوره ذوب خلاء باید مجهز به منبع تغذیه، سیستم کنترل و سیستم خنک کننده نیز باشد تا انرژی ورودی را برای تجهیزات ذوب مواد فراهم کند و مقدار مشخصی خنک کننده را در قسمت های کلیدی فراهم کند. برای جلوگیری از گرم شدن بیش از حد سیستم و در نتیجه کاهش عمر یا آسیب ساختاری. برای تجهیزات ذوب القایی با الزامات فرآیندی خاص، اجزای کمکی مرتبط وجود دارد، مانند چرخ دستی انتقال، باز و بسته شدن درب کوره، تشت ریخته گری گریز از مرکز، پنجره مشاهده و غیره. برای تجهیزات با ناخالصی های بیشتر، باید به فیلتر گاز نیز مجهز شود. سیستم و غیره مشاهده می شود که علاوه بر اجزای لازم، مجموعه کاملی از تجهیزات ذوب القایی نیز می توانند با افزودن اجزای دیگر مطابق با الزامات فرآیند خاص، عملکردهای مختلفی را محقق سازند و شرایط و روش های اجرایی مناسبی را برای آماده سازی فلز فراهم کنند.
2.1. کوره ذوب القایی خلاء
کوره ذوب القایی خلاء یک تجهیزات ذوب است که ابتدا فلز را با حرارت القایی در خلاء ذوب می کند و سپس فلز مایع را در قالب می ریزد تا شمش فلزی بدست آید. توسعه کوره های القایی خلاء در حدود سال 1920 آغاز شد و عمدتاً برای ذوب آلیاژهای نیکل-کروم استفاده می شد. تا زمانی که جنگ جهانی دوم پیشرفت فناوری خلاء را ترویج کرد، کوره ذوب القایی خلاء واقعاً توسعه یافته بود. در این دوره، به دلیل تقاضا برای مواد آلیاژی، کوره های ذوب القایی خلاء به مقیاس بزرگ، از چند تن اولیه تا ده ها تن کوره القایی فوق العاده بزرگ، ادامه دادند. به منظور انطباق با تولید انبوه، علاوه بر تغییر ظرفیت تجهیزات، ساختار کوره القایی نیز از یک کوره چرخه با یک چرخه به عنوان یک واحد به یک ذوب القایی خلاء پیوسته یا نیمه پیوسته برای شارژ، قالب تبدیل شده است. عملیات آماده سازی، ذوب و ریختن. عملکرد مداوم بدون توقف کوره باعث صرفه جویی در زمان شارژ و زمان انتظار برای خنک شدن شمش می شود. تولید مداوم باعث افزایش راندمان و همچنین افزایش خروجی آلیاژ می شود. بهتر است نیازهای تولید واقعی را برآورده کند. در مقایسه با کشورهای خارجی، کوره های القایی خلاء اولیه در کشور من ظرفیت نسبتا کمی دارند، عمدتاً زیر 2 تن. کوره های ذوب در مقیاس بزرگ همچنان به واردات از خارج وابسته هستند. با توسعه دهه های اخیر، کشور من همچنین می تواند ذوب القایی خلاء در مقیاس بزرگ را به تنهایی توسعه دهد. کوره، حداکثر ذوب به بیش از ده تن می رسد. کوره ذوب القایی خلاء VIM قبلاً با ساختار ساده، استفاده راحت و هزینه نگهداری کم توسعه یافته است و به طور گسترده در تولید واقعی استفاده شده است.
شکل اصلی کوره ذوب القایی خلاء. مواد فلزی از طریق یک برجک قابل چرخش به بوته ذوب اضافه می شوند. طرف دیگر با بوته هماهنگ است و اندازه گیری دما با قرار دادن ترموکوپل در فلز مذاب انجام می شود. فلز ذوب شده توسط مکانیزم چرخش رانده می شود و در قالب ریخته می شود تا ذوب فلز محقق شود. کل فرآیند کار ساده و راحت است. هر ذوب برای تکمیل نیاز به یک یا دو کارگر دارد. در طول فرآیند ذوب، نظارت بر دمای بلادرنگ و تنظیم ترکیب مواد قابل دستیابی است و مواد فلزی نهایی بیشتر با الزامات فرآیند مطابقت دارد.
2.2. کوره گازی غشایی القایی خلاء
برای مواد خاصی، نیازی به تکمیل ریختن در محفظه خلاء در فرآیند نیست، فقط حفظ حرارت و گاز زدایی در محیط خلاء مورد نیاز است. بر اساس کوره VIM، کوره گاز غشایی القایی خلاء کوره گاز زدایی VID به تدریج توسعه می یابد.
ویژگی اصلی کوره گاززدایی القایی خلاء ساختار فشرده و حجم کوچک کوره است. حجم کمتر برای استخراج سریع گاز و خلاء بهتر مساعدتر است. در مقایسه با کورههای گاز زدایی معمولی، این تجهیزات دارای حجم نسبتاً کم، کاهش دمای پایین، انعطافپذیری و اقتصاد بهتر است و برای تغذیه مایع یا جامد مناسب است. کوره VID را می توان برای ذوب و گاز زدایی فولادهای خاص و فلزات غیرآهنی استفاده کرد و باید در شرایط محیط جوی یا اتمسفر محافظ در قالب ریخته شود. کل فرآیند ذوب می تواند حذف ناخالصی هایی مانند کربن زدایی و پالایش مواد، هیدروژن زدایی، اکسید زدایی و گوگرد زدایی را محقق کند، که منجر به تنظیم دقیق ترکیب شیمیایی برای برآوردن نیازهای فرآیند می شود.
در شرایط خلاء خاص یا فضای محافظ، مواد فلزی به تدریج با حرارت دادن کوره گاززدایی القایی ذوب میشوند و گاز داخلی را میتوان در این فرآیند حذف کرد. اگر یک گاز واکنش مناسب در این فرآیند اضافه شود، با عنصر کربن در داخل فلز ترکیب میشود تا کاربیدهای گازی تولید شود که از کوره خارج میشوند و به هدف کربنزدایی و پالایش دست مییابند. در فرآیند ریختن، یک اتمسفر محافظ خاص باید وارد شود تا اطمینان حاصل شود که مواد فلزی که گاز زدایی شده است از گاز موجود در اتمسفر جدا شده است و در نهایت گاز زدایی و تصفیه مواد فلزی کامل می شود.
2.3. کوره ریختن گاز زدایی القایی خلاء
کوره ریختن گاز زدایی القایی خلاء بر اساس دو فناوری ذوب اول توسعه یافته است. در سال 1988، Leybold-Heraeus، سلف شرکت آلمانی ALD، اولین کوره VIDP را ساخت. هسته فنی این نوع کوره یک محفظه ذوب خلاء فشرده است که با بوته سیم پیچ القایی یکپارچه شده است. این فقط کمی بزرگتر از سیم پیچ القایی است و فقط حاوی سیم پیچ القایی و بوته است. کابل ها، خطوط لوله خنک کننده آب و مکانیزم گردش هیدرولیک همگی در خارج از محفظه ذوب نصب می شوند. مزیت آن محافظت از کابل ها و خطوط لوله خنک شونده با آب در برابر آسیب ناشی از پاشیدن فولاد مذاب و تغییرات دوره ای دما و فشار است. پوسته کوره VIDP به دلیل راحتی در جداسازی و تسهیل تعویض بوته، مجهز به سه بدنه کوره می باشد. پوشش کوره بوته آماده سازی چرخه تولید را کوتاه می کند و راندمان تولید را بهبود می بخشد.
پوشش کوره بر روی قاب کوره و دو ستون سیلندر هیدرولیک توسط خلاء آب بندی می شود. بلبرینگس هنگام ریختن، دو سیلندر هیدرولیک روی پوشش کوره در طرفین قرار می گیرند و پوشش کوره محفظه ذوب را به سمت خلاء هدایت می کند. بلبرینگ. در حالت ریزش مایل، هیچ حرکت نسبی بین محفظه ذوب و بوته سیم پیچ القایی وجود ندارد. رانر بخش مهمی از کوره VIDP است. از آنجایی که طراحی کوره VIDP، محفظه ذوب را از محفظه شمش جدا می کند، فولاد مذاب باید از طریق لوله خلاء وارد محفظه شمش شود. محفظه شمش با ضلع مایل مربع باز و بسته می شود. از دو بخش تشکیل شده است. قسمت ثابت در مجاورت محفظه رانر قرار دارد و قسمت متحرک به صورت افقی در امتداد مسیر زمین حرکت می کند تا باز و بسته شدن محفظه شمش کامل شود. در برخی تجهیزات، قسمت متحرک به صورت 30 درجه، باز به سمت چپ و راست به سمت بالا طراحی شده است که برای بارگیری و تخلیه قالب های شمش و نگهداری و تعمیر روزانه جرثقیل ها مناسب است. در ابتدای ذوب، بدنه کوره توسط مکانیزم هیدرولیک زیر بلند شده و به پوشش کوره ساختاری فوقانی کوره متصل شده و با مکانیزم خاصی قفل می شود. انتهای بالایی پوشش کوره از طریق خلاء به محفظه تغذیه متصل می شود دریچه.
از آنجایی که فقط قسمت ذوب در محفظه خلاء محصور شده و از طریق شیار انحراف به بیرون ریخته می شود، ساختار کوره فشرده است، محفظه ذوب کوچکتر است و خلاء را می توان بهتر و سریعتر کنترل کرد. در مقایسه با کوره ذوب القایی سنتی، دارای ویژگی های زمان تخلیه کوتاه و نرخ نشت کم است. کنترل فشار ایده آل را می توان با تجهیز سیستم کنترل منطقی PLC به دست آورد. در همان زمان، سیستم همزن الکترومغناطیسی می تواند به طور پایدار حوضچه مذاب را به هم بزند و عناصر اضافه شده به طور یکنواخت در حوضچه مذاب از بالا به پایین حل می شوند و دما را نزدیک به ثابت نگه می دارند. هنگام ریختن پول، رانر توسط سیستم گرمایش خارجی گرم می شود تا انسداد اولیه پورت ریختن و ترک حرارتی رانر کاهش یابد. با افزودن بافل فیلتر و سایر اقدامات، می تواند تاثیر فولاد مذاب را کاهش داده و خلوص فلز را بهبود بخشد. با توجه به حجم کم کوره VIDP، تشخیص نشتی خلاء و تعمیر آسانتر است و زمان تمیز کردن در کوره کوتاهتر است. علاوه بر این، دمای کوره را می توان با یک ترموکوپل کوچک و با قابلیت تعویض آسان اندازه گیری کرد.
2.4، بوته آب خنک القایی
روش ذوب معلق القایی الکترومغناطیسی بوته خنک شده با آب یک روش ذوبی است که در سال های اخیر به سرعت توسعه یافته است. عمدتاً برای تهیه مواد فلزی یا غیرفلزی با نقطه ذوب بالا، خلوص بالا و بسیار فعال استفاده می شود. با برش بوته مسی به قسمت های مساوی از ساختار گلبرگ مس، و خنک شدن آب از هر بلوک گلبرگ عبور می کند، این ساختار نیروی رانش الکترومغناطیسی را افزایش می دهد، به طوری که فلز مذاب در وسط فشرده می شود تا قوز تشکیل دهد و از گلبرگ جدا شود. دیوار بوته. این فلز در یک میدان الکترومغناطیسی متناوب قرار می گیرد. این دستگاه ظرفیت را در فضای حجمی داخل بوته متمرکز می کند و سپس یک جریان گردابی قوی روی سطح شارژ ایجاد می کند. از یک طرف گرمای ژول را آزاد می کند تا بار را ذوب کند و از طرف دیگر نیروی لورنتس را برای ذوب تشکیل می دهد. بدن معلق می شود و هم زدن قوی ایجاد می کند. عناصر آلیاژی اضافه شده را می توان به سرعت و به طور یکنواخت در مذاب مخلوط کرد و ترکیب شیمیایی را یکنواخت تر و هدایت دما را متعادل تر کرد. به دلیل اثر شناور مغناطیسی، مذاب با دیواره داخلی بوته تماس پیدا نمی کند که از آلودگی بوته به مذاب جلوگیری می کند. در عین حال، هدایت گرما را کاهش می دهد و تشعشع گرما را افزایش می دهد، که اتلاف حرارت فلز مذاب را کاهش می دهد و به دمای بالاتری می رسد. برای شارژ فلزی اضافه شده، می توان آن را با توجه به زمان و دمای تنظیم شده ذوب و گرم نگه داشت و شارژ نیازی به پردازش قبلی ندارد. ذوب بوته خنک شده با آب می تواند از نظر حذف اجزای فلزی و تصفیه گاز زدایی به سطح ذوب پرتو الکترونی برسد، در حالی که تلفات تبخیر کمتر است و مصرف انرژی کمتر است و راندمان تولید بهبود می یابد. با توجه به ویژگی های گرمایش غیر تماسی گرمایش القایی، تاثیر روی مذاب کمتر است و تأثیر خوبی در تهیه فلزات با خلوص بالاتر یا بسیار فعال دارد. با توجه به ساختار پیچیده تجهیزات، انجام ذوب maglev برای تجهیزات با ظرفیت بالا هنوز دشوار است. در این مرحله تجهیزات ذوب بوته مسی با ظرفیت بالا وجود ندارد. تجهیزات فعلی بوته خنک شده با آب فقط برای تحقیقات تجربی در مورد ذوب فلزات با حجم کم استفاده می شود.
3. روند توسعه آینده تجهیزات ذوب القایی
با توسعه فناوری گرمایش القایی خلاء، انواع کوره ها به منظور دستیابی به عملکردهای مختلف به طور مداوم در حال تغییر هستند. از یک ساختار ساده ذوبی یا گرمایشی، به تدریج به ساختار پیچیده ای تبدیل شده است که می تواند عملکردهای مختلف را تحقق بخشد و برای تولید مساعدتر است. برای فرآیندهای پیچیدهتر فناوری در آینده، نحوه دستیابی به کنترل دقیق فرآیند، اندازهگیری و استخراج اطلاعات مربوطه و کاهش هزینههای نیروی کار تا حد امکان، جهت توسعه تجهیزات ذوب القایی است.
3.1، مدولار
در یک مجموعه کامل از تجهیزات، اجزای مختلف برای نیازهای استفاده متفاوت مجهز شده اند. هر بخش از کامپوننت عملکرد خود را برای دستیابی به هدف استفاده خود انجام می دهد. برای انواع خاصی از کوره ها، افزودن ماژول های خاص برای کامل تر کردن تجهیزات، به عنوان مثال، مجهز به سیستم اندازه گیری دما کامل، به مشاهده تغییرات مواد در کوره با دما و دستیابی به کنترل معقول تر دما کمک می کند. مجهز به طیف سنج جرمی برای تشخیص ترکیب مواد، تنظیم زمان و ترتیب افزودن عناصر آلیاژی برای بهبود عملکرد آلیاژ در مرحله توسعه فرآیند. مجهز به تفنگ الکترونی و تفنگ یونی برای حل مشکل ذوب برخی فلزات نسوز و غیره. در تجهیزات متالورژی القایی آینده، ترکیبهای مختلف ماژولهای مختلف برای دستیابی به عملکردهای مختلف و برآورده کردن الزامات فرآیندی مختلف، به روند اجتنابناپذیر توسعه تبدیل شدهاند و همچنین ترکیب و مرجع زمینههای مختلف است. به منظور بهبود فرآیند ذوب فلز و به دست آوردن مواد با عملکرد بهتر، تجهیزات مدولار رقابت قوی تری در بازار خواهند داشت.
3.2. کنترل هوشمند
در مقایسه با ذوب سنتی، تجهیزات القایی خلاء مزیت بزرگی در تحقق کنترل فرآیند دارند. با توجه به توسعه فناوری رایانه، عملکرد دوستانه رابط انسان و ماشین، دریافت سیگنال هوشمند و تنظیم برنامه معقول در تجهیزات می تواند به راحتی به هدف کنترل فرآیند ذوب دست یابد، هزینه های نیروی کار را کاهش دهد و عملیات را ساده تر و ساده تر کند. راحت.
در توسعه آینده، سیستم های کنترل هوشمند تری به تجهیزات خلاء اضافه خواهند شد. برای فرآیند ایجاد شده، کنترل دقیق دمای ذوب از طریق سیستم کنترل هوشمند، افزودن مواد آلیاژی در زمان مشخص و تکمیل یک سری اقدامات ذوب، حفظ حرارت و ریختن برای افراد آسانتر خواهد بود. و همه اینها توسط رایانه کنترل و ضبط می شود و از تلفات غیر ضروری ناشی از خطاهای انسانی کاسته می شود. برای فرآیند ذوب مکرر، می تواند کنترل مدرن راحت تر و هوشمندانه تر را تحقق بخشد.
3.3. اطلاع رسانی
تجهیزات ذوب القایی مقدار زیادی اطلاعات ذوب را در طول کل فرآیند ذوب تولید می کنند، تغییرات پارامترهای بلادرنگ منبع تغذیه گرمایش القایی، میدان دمای شارژ، بوته، میدان الکترومغناطیسی تولید شده توسط سیم پیچ القایی، خواص فیزیکی مذاب فلز و غیره. در حال حاضر، تجهیزات فقط جمع آوری داده های ساده را انجام می دهند و فرآیند تجزیه و تحلیل پس از استخراج داده ها پس از تکمیل ذوب انجام می شود. در آینده، توسعه اطلاعات، جمعآوری و پردازش دادهها و فرآیند تحلیل به ناچار تقریباً با فرآیند ذوب هماهنگ خواهد شد. جمع آوری کامل داده ها برای مواد ذوب شده داخلی تجهیزات متالورژی، پردازش کامپیوتری داده ها، نمایش بیدرنگ میدان دمای داخلی و میدان الکترومغناطیسی تجهیزات تحت شرایط فعلی، و انتقال سیگنال، از طریق بازخورد بلادرنگ داده های مختلف، مناسب برای مردم مشاهده و تنظیم در زمان واقعی فرآیند ذوب دخالت و کنترل انسان را تقویت کرد. در فرآیند ذوب، تنظیمات به موقع برای بهبود فرآیند و بهبود عملکرد آلیاژ انجام می شود.
نتیجه گیری 4
با پیشرفت صنعت، فناوری ذوب القایی خلاء در دهههای اخیر با مزایای منحصر به فرد خود پیشرفت چشمگیری داشته است و نقش مهمی در صنعت دارد. در حال حاضر، اگرچه فناوری ذوب القایی خلاء کشور من هنوز از کشورهای خارجی عقب است، اما همچنان نیازمند تلاش بی وقفه متخصصان مربوطه برای بهبود رقابت در بازار تجهیزات ذوب ویژه کشورم است و تمام تلاش خود را برای تبدیل شدن به تجهیزات ذوب درجه یک در جهان می کند. . خط مقدم.
پیوند به این مقاله توسعه و روند فناوری ذوب القایی خلاء
بیانیه چاپ مجدد: اگر دستورالعمل خاصی وجود ندارد، تمام مقالات این سایت اصلی هستند. لطفا منبع چاپ مجدد را ذکر کنید: https://www.cncmachiningptj.com
PTJ® یک سازنده سفارشی است که طیف کاملی از میله های مس را ارائه می دهد. قطعات برنجی و قطعات مس. فرآیندهای تولید متداول عبارتند از بلنکینگ، منبت کاری، مسگری، خدمات EDM سیم، حکاکی، شکل گیری و خم شدن، ناراحت کننده، داغ جعل و پرس کردن، سوراخ کردن و پانچ کردن، نورد و خنثی کردن نخ، برش، ماشینکاری چند اسپیندل، اکستروژن و آهنگری فلزی و مهر زنی. کاربردها شامل میله های اتوبوس، هادی های الکتریکی، کابل های کواکسیال، موجبرها، اجزای ترانزیستور، لوله های مایکروویو، لوله های قالب خالی و متالورژی پودر مخازن اکستروژن
کمی در مورد بودجه پروژه و زمان تحویل مورد انتظار خود به ما بگویید. ما با شما استراتژی خواهیم داشت تا مقرون به صرفه ترین خدمات را برای کمک به شما در دستیابی به هدف خود ارائه دهیم، می توانید مستقیماً با ما تماس بگیرید ( sales@pintejin.com ).
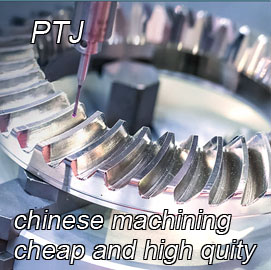
- ماشینکاری 5 محور
- تراش تراش
- چرخش CNC
- صنایع ماشینکاری
- فرآیند ماشینکاری
- درمان سطحی
- ماشینکاری فلز
- ماشینکاری پلاستیک
- قالب متالورژی پودر
- قالب ریخته گری
- گالری قطعات
- قطعات فلزی خودرو
- قطعات ماشین آلات
- LED هیت سینک
- قطعات ساختمان
- قطعات موبایل
- قطعات پزشکی
- قطعات الکترونیکی
- ماشینکاری خیاطی
- قطعات دوچرخه
- ماشینکاری آلومینیوم
- ماشینکاری تیتانیوم
- ماشینکاری فولاد ضد زنگ
- ماشینکاری مس
- ماشینکاری برنجی
- ماشینکاری فوق آلیاژی
- ماشین کاری پیک
- ماشینکاری UHMW
- ماشینکاری یک طرفه
- ماشینکاری PA6
- ماشینکاری PPS
- ماشینکاری تفلون
- ماشینکاری اینکونل
- ماشینکاری فولاد ابزار
- مواد بیشتر