تجزیه و تحلیل روند توسعه جدید فناوری عملیات حرارتی برای اتصال دهنده های خودرو
1. تاثیر فرآیند عملیات حرارتی بر بهبود استحکام خستگی پیچ و مهره ها
برای مدت طولانی، خودرو بستویژگی های اساسی طیف وسیعی از انواع، انواع و مشخصات بر آن ها غالب بوده است. انتخاب و استفاده از آن شامل تجزیه و تحلیل ساختاری، طراحی اتصال، تجزیه و تحلیل خرابی و خستگی، الزامات خوردگی و روشهای مونتاژ است و این عوامل کیفیت نهایی و قابلیت اطمینان محصولات خودرو را تا حد زیادی تعیین میکنند.
عمر خستگی پیچ و مهره های خودرو با استحکام بالا همیشه یک موضوع مهم بوده است. داده ها نشان می دهد که بیشتر خرابی پیچ ها ناشی از خرابی خستگی است و تقریباً هیچ نشانه ای از خرابی خستگی پیچ وجود ندارد. بنابراین، احتمال وقوع حوادث بزرگ در هنگام شکست خستگی وجود دارد. عملیات حرارتی می تواند خواص مواد اتصال دهنده را بهینه کند و استحکام خستگی آنها را افزایش دهد. با توجه به نیاز روزافزون استفاده از پیچ و مهره های با استحکام بالا، بهبود استحکام خستگی مواد پیچ از طریق عملیات حرارتی اهمیت بیشتری دارد.
1. شروع ترک های خستگی در مواد
محلی که ترک خستگی برای اولین بار شروع می شود، منبع خستگی نامیده می شود. منبع خستگی به ریزساختار پیچ بسیار حساس است و میتواند باعث ایجاد ترکهای خستگی در مقیاس بسیار کوچک شود، معمولاً در اندازههای 3 تا 5 دانه. کیفیت سطح پیچ مشکل اصلی است. منشا خستگی، بیشتر خستگی از سطح پیچ یا زیر سطح شروع می شود. تعداد زیادی نابجایی، برخی از عناصر آلیاژی یا ناخالصیها در کریستال مواد پیچ و تفاوت در استحکام مرزی دانهها ممکن است منجر به شروع ترک خستگی شود. مطالعات نشان دادهاند که ترکهای خستگی در مکانهای زیر مستعد ایجاد میشوند: مرز دانهها، آخالهای سطحی یا ذرات فاز دوم، و حفرهها. این مکان ها همگی به ریزساختار پیچیده و متغیر مواد مربوط می شوند. اگر بتوان ریزساختار را پس از عملیات حرارتی بهبود بخشید، استحکام خستگی مواد پیچ را می توان تا حد معینی بهبود بخشید.
2. تاثیر کربن زدایی بر قدرت خستگی
کربن زدایی سطح پیچ باعث کاهش سختی سطح و مقاومت در برابر سایش پیچ پس از خاموش شدن می شود و مقاومت خستگی پیچ را به میزان قابل توجهی کاهش می دهد. تست کربن زدایی برای عملکرد پیچ در استاندارد GB/T3098.1 وجود دارد و حداکثر عمق کربن زدایی مشخص شده است. هنگام تجزیه و تحلیل دلایل خرابی پیچ هاب 35CrMo، مشخص شد که در محل اتصال رزوه و میله یک لایه کربن زدایی وجود دارد. Fe3C می تواند با O2، H2O و H2 در دماهای بالا واکنش نشان دهد تا Fe3C در مواد پیچ را کاهش دهد، در نتیجه فاز فریت مواد پیچ را افزایش داده، استحکام مواد پیچ را کاهش می دهد و به راحتی باعث ایجاد ریزترک می شود. در فرآیند عملیات حرارتی دمای گرمایش باید به خوبی کنترل شود و در عین حال از گرمایش حفاظتی جوی قابل کنترل برای رفع این مشکل استفاده شود.
3. تأثیر عملیات حرارتی بر قدرت خستگی
تمرکز تنش روی سطح پیچ استحکام سطح آن را کاهش می دهد. هنگامی که تحت بارهای دینامیکی متناوب قرار می گیرد، فرآیند ریز تغییر شکل و بازیابی در قسمت تمرکز تنش بریدگی ادامه خواهد داشت و تنش دریافتی بسیار بیشتر از قسمت بدون تمرکز تنش است، بنابراین به راحتی می توان به آن منجر شد. نسل ترک های خستگی
اتصال دهنده ها برای بهبود ریزساختار تحت عملیات حرارتی و حرارتی قرار می گیرند و دارای خواص مکانیکی جامع عالی هستند که می تواند استحکام خستگی مواد پیچ را بهبود بخشد، اندازه دانه را به طور منطقی کنترل کند تا از انرژی ضربه ای در دمای پایین اطمینان حاصل شود، و همچنین چقرمگی ضربه بالاتری به دست آورد. عملیات حرارتی معقول برای پالایش دانه ها و کوتاه کردن فاصله بین مرزهای دانه می تواند از ترک های ناشی از خستگی جلوگیری کند. اگر مقدار مشخصی سبیل یا ذرات ثانویه در ماده وجود داشته باشد، این فازهای اضافه شده می توانند تا حدی از لغزش ساکن جلوگیری کنند. لغزش تسمه از شروع و گسترش ریزترک ها جلوگیری می کند.
2. خاموش کردن محیط و محیط پردازش برای عملیات حرارتی
اتصال دهنده های خودرو با استحکام بالا دارای یک سری ویژگی های فنی هستند: درجه با دقت بالا. شرایط خدمات شدید، در تمام طول سال به همراه میزبان در برابر نفوذ سرمای شدید و اختلاف دمای شدید مقاومت می کند و در برابر فرسایش دماهای بالا و پایین مقاومت می کند. بار استاتیکی، بار دینامیکی، اضافه بار، بار سنگین و خوردگی محیطی محیطی، علاوه بر اثر بار کششی پیش انقباض محوری، تحت بارهای متناوب کششی اضافی، بارهای متناوب برشی عرضی یا بارهای خمشی ترکیبی در حین کار قرار خواهد گرفت. گاهی اوقات نیز در معرض بارهای ضربه ای قرار می گیرد. بارهای متناوب عرضی اضافی می توانند باعث شل شدن پیچ ها شوند، بارهای متناوب محوری می توانند باعث شکستگی خستگی پیچ ها شوند و بارهای کششی محوری می توانند باعث شکستگی تاخیری پیچ ها و همچنین شرایط دمای بالا شوند. خزش پیچ و مهره و غیره
تعداد زیادی از پیچ های شکست خورده نشان می دهد که در طول انتقال بین سر پیچ و پیچ شکسته شده اند محور در حین خدمت؛ آنها در امتداد محل اتصال رزوه پیچ کشیده شدند محور و محور; و سگک های کشویی در امتداد قسمت نخ دار وجود داشت. تجزیه و تحلیل متالوگرافی: وجود فریت حل نشده بیشتر در سطح و هسته پیچ و آستنیته شدن ناکافی در هنگام کوئنچ، استحکام ماتریس ناکافی و تمرکز تنش یکی از دلایل مهم خرابی است. به همین دلیل، برای اطمینان از سخت شدن سطح مقطع پیچ و یکنواختی سازه، پیوند بسیار مهمی است.
عملکرد روغن خاموش کننده این است که به سرعت گرمای پیچ های فلزی داغ را از بین می برد و آنها را تا دمای تبدیل مارتنزیت کاهش می دهد تا ساختار مارتنزیت با سختی بالا و عمق لایه سخت شده به دست آید. در عین حال، باید کاهش تغییر شکل پیچ و جلوگیری از ترک خوردگی را نیز در نظر گرفت. بنابراین، مشخصه اصلی روغن خاموش کننده، "ویژگی خنک کننده" است که با سرعت خنک شدن سریعتر در مرحله دمای بالا و سرعت خنک شدن کندتر در مرحله دمای پایین مشخص می شود. این ویژگی برای نیازهای خاموش کردن فولاد ساختاری آلیاژی پیچ و مهره های با مقاومت بالا ≥ 10.9 بسیار مناسب است.
روغن خاموش کننده سریع در حین استفاده باعث تجزیه حرارتی، اکسیداسیون و واکنش های پلیمریزاسیون می شود که منجر به تغییرات در ویژگی های خنک کننده می شود. رطوبت کمیاب در روغن به طور جدی بر عملکرد خنک کننده روغن تأثیر می گذارد و در نتیجه باعث کاهش روشنایی و سختی ناهموار بست ها پس از خاموش شدن می شود. ایجاد لکه های نرم یا حتی تمایل به ترک خوردن. مطالعات نشان داده است که مشکلات تغییر شکل ناشی از خاموش کردن روغن تا حدی ناشی از آب موجود در روغن است. علاوه بر این، محتوای آب موجود در روغن نیز امولسیون شدن و فاسد شدن روغن را تسریع می کند و باعث از بین رفتن مواد افزودنی در روغن می شود. هنگامی که محتوای آب در روغن بیشتر یا مساوی 0.1٪ باشد، زمانی که روغن گرم می شود، آب جمع شده در کف مخزن روغن ممکن است ناگهان حجم خود را افزایش دهد، که ممکن است باعث سرریز شدن روغن از مخزن کوئنچینگ شود و باعث شود. یک آتش سوزی
برای روغن خاموش کننده سریع مورد استفاده در کوره تسمه مشبک پیوسته، بر اساس داده های ویژگی های خاموشی جمع آوری شده در آزمون فاصله 3 ماهه، می توان پایداری و ویژگی های خاموش کننده روغن را تعیین کرد، عمر مفید کوئنچ را تعیین کرد. روغن، و عملکرد روغن خاموش کننده را پیش بینی کنید. مشکلات مربوط به تغییر، در نتیجه کاهش دوباره کاری یا تلفات ناشی از تغییرات در خواص روغن خاموش کردن، آن را به یک روش کنترل مرسوم برای تولید تبدیل می کند. عمق سخت شدن مستقیماً بر کیفیت پیچ پس از عملیات حرارتی تأثیر می گذارد. هنگامی که سختی پذیری مواد ضعیف است، سرعت خنک کننده محیط خنک کننده آهسته است، و اندازه پیچ بزرگ است، هسته پیچ نمی تواند در طول کوئنچ کردن به مارتنزیت تبدیل شود. سازمان سطح قدرت ناحیه قلب، به ویژه قدرت تسلیم را کاهش می دهد. بدیهی است که این برای پیچ و مهره هایی که تنش کششی توزیع یکنواختی را در طول کل مقطع متحمل می شوند بسیار زیان آور است. سختی ناکافی استحکام را کاهش می دهد. بررسی متالوگرافی نشان داد که فریت پروتکتوئیدی و ساختارهای فریت مشبکی در هسته وجود دارد که نشان میدهد سختشدگی پیچ باید تقویت شود. همانطور که همه ما می دانیم، دو راه برای افزایش سختی برای افزایش دمای کوئنچ وجود دارد. سختی پذیری محیط خاموش کننده را افزایش می دهد، که می تواند به طور موثر عمق سخت شدن پیچ را افزایش دهد.
Houghto-Quench به ویژه روغن خاموش کننده سریع را بر اساس روغن خاموش کننده اصلی با سرعت متوسط، Houghto-Quench G، توسعه داده است. عمق سخت شدن رضایت بخش
مرحله فیلم بخار روغن خاموش کننده سریع کوتاه است، یعنی مرحله دمای بالا روغن به سرعت خنک می شود. این ویژگی برای به دست آوردن یک لایه سخت تر برای پیچ و مهره های M10 فولادی 33B45 و 20 ≤ M42 و مهره های M35 مفید است، در حالی که برای فولادهای SWRCH10K و 28B12، تنها زمانی که ضخامت کمتر یا مساوی با پیچ و مهره M30 و مهره M90 باشد، سختی کاهش می یابد. هسته و سختی سطح تفاوت کمی دارند. از تجزیه و تحلیل توزیع سرعت خنکسازی، علاوه بر خنکسازی سریع مورد نیاز در مراحل دمایی میانی و بالا، نرخ خنکسازی در دمای پایین روغن تأثیر بیشتری بر عمق لایه سختشده دارد. هرچه سرعت خنکسازی در دمای پایین بیشتر باشد، لایه سختشده عمیقتر میشود. این برای اتصال دهنده های با استحکام بالا بسیار سودمند است تا بار را به طور یکنواخت در کل بخش تحمل کنند، و لازم است که حدود 20٪ ساختار مارتنزیت را قبل از تلطیف در حالت خاموش به دست آورید. شاخص های ارزیابی شامل نزدیک به XNUMX شاخص مانند نقطه اشتعال، ویسکوزیته، مقدار اسید، مقاومت در برابر اکسیداسیون، کربن باقیمانده، خاکستر، لجن، سرعت خنک کننده خاموش، و روشنایی خاموش شدن است.
برای پیچ و مهره های سایز بزرگتر، عامل خاموش کننده PAG راه حل اصلی است که نیازهای خاموش کننده اکثر محصولات را برآورده می کند. عامل خاموش کننده PAG در منطقه تبدیل مارتنزیت در مرحله جوش است و سرعت خنک کننده بالا است و خطر بیشتری وجود دارد. با تمرکز قابل تنظیم است. میزان سرمایش در شاخص کلیدی حدود 300 درجه است. هرچه سرعت خنکسازی در این نقطه دما کمتر باشد، توانایی قویتر برای جلوگیری از فرونشاندن ترکها و نمرات فولاد مناسبتر است. پایداری سرعت سرمایش همرفتی در حین استفاده مهمترین عامل برای اطمینان از کیفیت کوئنچ است.
در نمونه پیچ های شکست اولیه مشاهده می شود که ایرادهای ترک بر روی رزوه پیچ های شکسته نزدیک شکستگی وجود دارد. دلیل اصلی این است که پیچ ها به درستی رول نشده اند. ناشی از تا شدن؛ ترکهای ریز با اعماق مختلف نیز در پایین نخ دیده میشوند و تومور ساختهشده در ماشینکاری ناحیه تمرکز تنش را تشکیل میدهد. استاندارد GB/T5770.3-2000 «الزامات ویژه برای پیچها، پیچها و ناودانیهای دارای عیوب سطحی روی اتصالدهندهها» تصریح میکند که چینهایی که بیش از یک چهارم ارتفاع پروفیل رزوه بالاتر از قطر گام پیچها تحت تنش نیستند، باید باشند. مجاز است تا کردن و ساخته شدن کف رزوه، عیب مجاز نیست و تا شدن یکی از دلایل اصلی شکستگی پیچ است. استفاده از روان کننده فشار شدید Houghton برای پردازش رزوه پیچ می تواند به طور موثر از ایجاد لبه جلوگیری کند و تمرکز استرس را کاهش دهد و در نتیجه به بهبود عمر خستگی پیچ کمک کند.
3. حفاظت از سطح و توسعه فناوری اتصال دهنده های خودرو
بست های خودرو به ویژه پیچ های بست، گیره های لوله، گیره های الاستیک و غیره در هنگام استفاده در محیط های بسیار سخت قرار دارند و معمولاً به شدت خورده می شوند و حتی به دلیل زنگ زدگی به سختی از هم جدا می شوند. بنابراین، بست ها باید خواص ضد خوردگی خوبی داشته باشند. متداولترین روشهایی که در حال حاضر استفاده میشوند عبارتند از: الکتروگالوانیزه کردن، آلیاژ روی نیکل، فسفاته کردن، سیاهکردن و عملیات داکرومت روی سطح. با توجه به محدودیت محتوای کروم شش ظرفیتی در پوشش سطحی بست های خودرو، استانداردهای دستورالعمل های حفاظت از محیط زیست را رعایت نمی کند و محصولات حاوی مواد مضر مجاز به ورود به بازار نمی باشد که این امر در نوآوری ها به سطح بی سابقه ای رسیده است. توانایی بست خودرو درمان سطح الزامات استاندارد محیطی
1. روکش روی آلومینیومی مبتنی بر آب Geomet
فناوری پوشش جدید سازگار با محیط زیست- روکش فلزی روی و آلومینیوم Geomet، گروه Enoufu یک فناوری کامل را بر اساس بیش از 30 سال تجربه فناوری ضد زنگ سطح DACROMET و پس از سال ها تحقیق و توسعه توسعه داده است. تکنولوژی جدید تصفیه سطح کروم --- GEOMET.
مکانیسم ضد زنگ، ساختار فیلم درمان شده توسط Gummet نیز مانند فیلم درمان شده توسط Dacromet است. ورق های فلزی در لایه ها روی هم قرار می گیرند تا یک لایه ترکیب شده با یک چسب مبتنی بر سیلیکون برای پوشاندن بستر تشکیل شود.
مزایای ژئومت: رسانایی، ورق فلزی با استحکام بالا باعث رسانایی پیچهای Geomet میشود. سازگاری با رنگ، Geomet می تواند به عنوان یک آستر برای اکثر رنگ ها از جمله آبکاری استفاده شود. محلول حفاظت از محیط زیست، محلول مبتنی بر آب، فاقد کروم است و آب فاضلاب تولید نمی شود و هیچ ماده مضری در هوا تخلیه نمی شود. مقاومت در برابر خوردگی عالی، ضخامت فیلم تنها 6-8μm، می تواند به آزمایش اسپری نمک بیش از 1000 ساعت برسد. مقاومت در برابر حرارت، فیلم معدنی، و فیلم حاوی رطوبت نیست. فرآیند شکنندگی بدون هیدروژن، فرآیند پوشش بدون اسید و الکترولیتی، مانند فرآیند آبکاری معمولی از شکنندگی هیدروژن اجتناب کنید.
پایداری ضریب اصطکاک برای مونتاژ بست های خودرو بسیار مهم است. پوشش روی و آلومینیوم پوسته پوسته مبتنی بر آب راه حلی برای ضریب اصطکاک است. بر اساس پوشش روی-آلومینیوم، یک پوشش سطح معدنی مبتنی بر آب با عملکرد روانکاری ---PLUS اعمال می شود.
2. تکنولوژی پوشش الکتروفورتیک
در سال های اخیر برخی از بست های برخی از شرکت های خودروسازی از پوشش الکتروفورتیک به جای غیرفعال سازی پس از آبکاری استفاده می کنند. به عبارت ساده، اصل پوشش الکتروفورتیک این است که "جنس مخالف یکدیگر را جذب می کنند" که مانند آهنربا است. الکتروفورز آند با پیچ و مهره روی آند پوشانده می شود و رنگ دارای بار منفی است. در حالی که الکتروفورز کاتدی با پیچ و مهره روی کاتد پوشانده می شود، رنگ دارای بار مثبت است. همانطور که همه ما می دانیم، پوشش الکتروفورتیک بسیار مکانیزه، سازگار با محیط زیست است و لایه رنگ دارای مقاومت در برابر خوردگی عالی است. بازیافت و استفاده مجدد از منابع آب برای کاهش انتشار گازهای گلخانه ای؛ تقویت بازیافت فلزات سنگین برای کاهش انتشار کاهش انتشار VOC (ترکیبات آلی فرار)؛ کاهش مصرف انرژی (آب، برق، سوخت و غیره)، و برآورده کردن الزامات حفاظت از محیط زیست برای کاهش هزینه ها و بهبود کیفیت.
چندین سال است که برای قطعات خودرو و اتصال دهنده ها اعمال می شود. فرآیند پوشش الکتروفورتیک نسبتاً بالغ است. محصولی است که جایگزین آبکاری می شود. PPGElect ropolyseal بست مواد پوشش الکتروفورتیک ویژه، الکتروفورز آند EPll/SST 120 تا 200 ساعت، الکتروفورز کاتدی EPll/SST 200 تا 300 ساعت، EPlV/SST 500 × 1000 ساعت، الکتروفورز کاتدیک 1000 ساعت، الکتروفورز کاتدیک 1500 ساعت و ZiNC Rich پوشش پوشش آلی غنی از روی (رسانا).
با پیشرفت تکنولوژی، علاوه بر پوشش الکتروفورتیک کاتدی با مقاومت در برابر خوردگی عالی، پوشش الکتروفورتیک آندی با مقاومت هوای معین و پوشش الکتروفورتیک کاتدی با مقاومت در برابر خوردگی لبه نیز عملاً در خط تولید اعمال شده است. در حال حاضر، سری پوشش الکتروفورتیک PPG توسط بسیاری از شرکت های خودروسازی تایید شده است، و یک سری مشخصات به یک استاندارد یکپارچه تغییر یافته است، S424 به S451 تغییر یافته است، مانند Ford WSS-M21P41-A2، S451. جنرال موتورز GM6047 کد G; کرایسلر PS-7902 Mcthod C.
مزایای پوشش الکتروفورتیک برای حفاظت از محیط زیست مفید است. پوشش الکتروفورتیک از رنگ مبتنی بر آب استفاده می کند و غیرفعال سازی از کروم سه ظرفیتی استفاده می کند. بهبود مقاومت در برابر خوردگی محصول، چسبندگی عالی؛ بدون سوراخ پلاگین، بدون نخ پیچ، ضخامت فیلم یکنواخت، مقدار گشتاور ثابت. آبکاری سنتی + فرآیند غیرفعال سازی، آزمایش اسپری نمک به حدود 144 ساعت می رسد. پس از اتخاذ روی فسفاته + پرایمر غنی از روی + فرآیند پوشش الکتروفورتیک کاتدی، آزمایش اسپری نمک می تواند به بیش از 1000 ساعت برسد، اگر فرآیند آبکاری + الکتروفورتیک کاتدی اتخاذ شود، آزمایش اسپری نمک می تواند به بیش از 500 ساعت برسد.
4 ، نتیجه گیری
در آینده، توسعه اتصال دهندههای خودرو شخصیتر خواهد شد، فرآیندهای عملیات حرارتی در ویژگیهای خدمات برجستهتر خواهند بود و فناوریهای هوشمند، سبز و سبک وزن همگی نقش مهمی را ایفا خواهند کرد. توسعه فناوری و تجهیزات پایه و اساس توسعه تولید پیشرفته است و هنوز جای زیادی برای توسعه وجود دارد. برای کم کردن فاصله با سطح پیشرفته کشورهای خارجی، کار هنوز بسیار دشوار است و کار سنگین و طولانی است.
پیوند به این مقاله تجزیه و تحلیل روند توسعه جدید فناوری عملیات حرارتی برای اتصال دهنده های خودرو
بیانیه چاپ مجدد: اگر دستورالعمل خاصی وجود ندارد، تمام مقالات این سایت اصلی هستند. لطفا منبع چاپ مجدد را ذکر کنید: https://www.cncmachiningptj.com
PTJ® یک سازنده سفارشی است که طیف کاملی از میله های مس را ارائه می دهد. قطعات برنجی و قطعات مس. فرآیندهای تولید متداول عبارتند از بلنکینگ، منبت کاری، مسگری، خدمات EDM سیم، حکاکی، شکل گیری و خم شدن، ناراحت کننده، داغ جعل و پرس کردن، سوراخ کردن و پانچ کردن، نورد و خنثی کردن نخ، برش، ماشینکاری چند اسپیندل، اکستروژن و آهنگری فلزی و مهر زنی. کاربردها شامل میله های اتوبوس، هادی های الکتریکی، کابل های کواکسیال، موجبرها، اجزای ترانزیستور، لوله های مایکروویو، لوله های قالب خالی و متالورژی پودر مخازن اکستروژن
کمی در مورد بودجه پروژه و زمان تحویل مورد انتظار خود به ما بگویید. ما با شما استراتژی خواهیم داشت تا مقرون به صرفه ترین خدمات را برای کمک به شما در دستیابی به هدف خود ارائه دهیم، می توانید مستقیماً با ما تماس بگیرید ( sales@pintejin.com ).
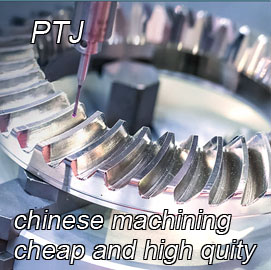
- ماشینکاری 5 محور
- تراش تراش
- چرخش CNC
- صنایع ماشینکاری
- فرآیند ماشینکاری
- درمان سطحی
- ماشینکاری فلز
- ماشینکاری پلاستیک
- قالب متالورژی پودر
- قالب ریخته گری
- گالری قطعات
- قطعات فلزی خودرو
- قطعات ماشین آلات
- LED هیت سینک
- قطعات ساختمان
- قطعات موبایل
- قطعات پزشکی
- قطعات الکترونیکی
- ماشینکاری خیاطی
- قطعات دوچرخه
- ماشینکاری آلومینیوم
- ماشینکاری تیتانیوم
- ماشینکاری فولاد ضد زنگ
- ماشینکاری مس
- ماشینکاری برنجی
- ماشینکاری فوق آلیاژی
- ماشین کاری پیک
- ماشینکاری UHMW
- ماشینکاری یک طرفه
- ماشینکاری PA6
- ماشینکاری PPS
- ماشینکاری تفلون
- ماشینکاری اینکونل
- ماشینکاری فولاد ابزار
- مواد بیشتر