راهنمای جامع نحوه راه اندازی ابزار برش تراش
راه اندازی ابزار برش تراش یک مهارت اساسی برای هر ماشینکاری است، به خصوص در هنگام کار با ماشین های تراشکاری کنترل عددی کامپیوتری (CNC). تنظیم مناسب ابزار برای دستیابی به نتایج دقیق و دقیق ماشین کاری بسیار مهم است. در این راهنمای جامع، به جزئیات پیچیده نحوه راه اندازی ابزار برش تراش برای تراشکاری CNC خواهیم پرداخت. از اصول اجزای ابزار تراش گرفته تا تکنیک های پیشرفته برای بهینه سازی عملکرد برش، هدف این مقاله ارائه یک درک جامع از فرآیند است. در پایان این راهنما، دانش و مهارت های لازم برای راه اندازی ابزار برش تراش با اطمینان و دقت را خواهید داشت و از نتایج بهینه در عملیات تراشکاری CNC خود اطمینان حاصل می کنید.
آشنایی با ابزارهای برش تراش
در دنیای ماشینکاری، ابزارهای برش تراش اجزای ضروری برای شکل دادن و تبدیل مواد خام به قطعات مهندسی دقیق هستند. چه با ماشینهای تراش دستی سنتی یا ماشینهای تراشکاری پیشرفته CNC کار میکنید، داشتن درک کامل از ابزارهای برش تراش ضروری است. در این بخش به بررسی ویژگی ها، عملکردها و انواع ابزارهای برش تراش خواهیم پرداخت.
ویژگی های ابزار برش تراش
ابزارهای برش تراش برای انجام انواع عملیات ماشینکاری مانند تراشکاری، روکشی، شیارکاری، رزوه کشی و غیره طراحی شده اند. این ابزارها چندین ویژگی مشترک دارند:
- سختی: ابزارهای برش تراش معمولاً از فولاد پرسرعت (HSS)، کاربید یا سایر مواد ابزار تخصصی ساخته می شوند. این مواد به دلیل سختی انتخاب شدهاند و به ابزار اجازه میدهند در برابر دماها و فشارهای بالا که در حین برش ایجاد میشوند مقاومت کنند.
- لبه برش: لبه برش ابزار تراش قسمتی است که در واقع مواد را از قطعه کار جدا می کند. این ابزار به گونه ای تیز و دقیق طراحی شده است و هندسه لبه برش می تواند بسته به وظیفه خاصی که ابزار برای آن در نظر گرفته شده است متفاوت باشد.
- ساقه: ساقه ابزار تراش قسمتی است که به جا ابزار گیره می شود. پایداری و استحکام ابزار را در طول کار فراهم می کند فرآیند ماشینکاری. طرح های ساق می تواند بر اساس نوع ابزار و مشخصات سازنده متفاوت باشد.
- نگهدارنده ابزار: نگهدارنده ابزار جزء مهمی است، به ویژه در تراشکاری CNC، زیرا به طور ایمن ابزار تراش را در جای خود نگه می دارد. برای اطمینان از عملکرد بهینه ابزار، باید ثبات، دقت و سهولت تنظیم را فراهم کند.
- هندسه: هندسه ابزار برش شامل زاویه چنگک، زاویه فاصله و تراشه شکن نقش بسزایی در تعیین عملکرد ابزار دارد. هندسه مناسب برای دستیابی به حذف کارآمد مواد و تخلیه تراشه ضروری است.
- پوشش: بسیاری از ابزارهای برش تراش با پوشش های تخصصی مانند TiN (نیترید تیتانیوم) یا TiAlN (نیترید آلومینیوم تیتانیوم)، برای افزایش عمر ابزار، کاهش اصطکاک و بهبود عملکرد عرضه می شوند.
توابع ابزارهای برش تراش
ابزارهای برش تراش چندین عملکرد اساسی را در فرآیند ماشینکاری انجام می دهند:
- حذف مواد: وظیفه اصلی ابزارهای برش تراش، حذف مواد از قطعه کار است. این حذف می تواند از طریق چرخاندن (چرخش قطعه کار در حین برش)، رو به رو شدن (ایجاد یک سطح صاف) یا سایر عملیات رخ دهد.
- کنترل ابعادی: ابزارهای برش وظیفه دارند از مطابقت ابعاد قطعه ماشینکاری شده با مشخصات مورد نظر اطمینان حاصل کنند. کنترل دقیق برای دستیابی به نتایج دقیق و ثابت ضروری است.
- سطح پایان: کیفیت پرداخت سطح بر اساس تیز بودن ابزار برش، هندسه و پارامترهای برش استفاده شده تعیین می شود. یک ابزار برش که به خوبی نگهداری شده و به درستی تنظیم شده باشد به یک سطح صاف و ظریف کمک می کند.
- کنترل تراشه: کنترل موثر تراشه برای جلوگیری از تجمع تراشه و حفظ محیط کاری تمیز و ایمن ضروری است. تراشه شکن در برخی ابزارها به تسهیل برداشتن تراشه کمک می کند.
- بهره وری: ابزارهای برش تراش به گونه ای طراحی شده اند که فرآیندهای ماشینکاری را کارآمد و مقرون به صرفه کنند. آنها به به حداقل رساندن ضایعات مواد و بهینه سازی عمر ابزار کمک می کنند و هزینه های تولید را کاهش می دهند.
انواع ابزار برش تراش
ابزارهای برش تراش در انواع مختلفی موجود هستند که هر کدام برای کارهای ماشینکاری خاص طراحی شده اند. در اینجا چند نوع رایج وجود دارد:
- ابزارهای تراشکاری: این ابزارها همه کاره هستند و برای عملیات تراشکاری استوانه ای استفاده می شوند. آنها می توانند سطوح خارجی و داخلی یک قطعه کار را شکل دهند.
- ابزار خسته کننده: ابزارهای حفاری برای بزرگ کردن یا تکمیل سوراخ های موجود استفاده می شوند. آنها برای دقت و دقت در ماشینکاری سوراخ طراحی شده اند.
- ابزار جداسازی: ابزار جداسازی برای جدا کردن یک قطعه کار از یک استوک بزرگتر استفاده می شود. آنها خطوط جداکننده تعریف شده را با حداقل ضایعات ایجاد می کنند.
- ابزار نخ زنی: ابزار رزوه کشی برای برش نخ روی قطعه کار استفاده می شود. آنها در اشکال و اندازه های مختلف برای نیازهای مختلف رزوه وجود دارند.
- ابزار شیارکاری: ابزارهای شیار زنی شیارها یا فرورفتگی هایی روی قطعه کار ایجاد می کنند که معمولاً برای قرار دادن حلقه های O، حلقه های نگهدارنده یا سایر ویژگی ها است.
- ابزارهای مواجهه: ابزارهای روکش برای ایجاد سطوح صاف در انتهای قطعه کار طراحی شده اند. آنها اغلب برای دستیابی به سطوح عمود بر هم یا حذف مواد از انتهای قطعه کار استفاده می شوند.
درک ویژگی ها و عملکرد ابزارهای برش تراش برای انتخاب ابزار مناسب برای یک کار ماشینکاری خاص ضروری است. انتخاب ابزار برش می تواند به طور قابل توجهی بر کیفیت و کارایی فرآیند ماشینکاری تأثیر بگذارد و آن را به یک تصمیم مهم در هر عملیات تراش تبدیل کند. بعلاوه، تعمیر و نگهداری مناسب و راه اندازی ابزار برای اطمینان از نتایج ثابت و دقیق حیاتی است، که در ادامه این راهنما با جزئیات بیشتر مورد بحث قرار خواهد گرفت.
انواع ابزار برش تراش
ابزارهای برش تراش انواع مختلفی دارند که هر کدام به طور خاص برای کار ماشینکاری خاصی طراحی شده اند. درک این انواع مختلف ابزارهای برش و کاربرد آنها برای انتخاب ابزار مناسب برای یک کار ضروری است. در اینجا چند نوع رایج از ابزارهای برش تراش آورده شده است:
ابزارهای تراشکاری:
- ابزار بینی گرد: برای عملیات تراشکاری همه منظوره استفاده می شود. دارای لبه برش گرد است و برای هر دو برش خشن و تکمیل مناسب است.
- ابزار الماس: این لبه به دلیل لبه برش الماس شکل آن نامگذاری شده است و برای ماشینکاری دقیق بر روی مواد مختلف از جمله فلزات و پلاستیک ایده آل است.
- ابزار بینی مربعی: دارای لبه برش مربعی است و معمولاً برای عملیات چرخش رو به رو و شانه استفاده می شود.
ابزار خسته کننده:نوار حفاری داخلی: برای بزرگ کردن و تکمیل سوراخ های موجود در قطعه کار استفاده می شود. این برای دقت طراحی شده است و می تواند ابعاد داخلی دقیق ایجاد کند.
ابزار جداسازی:تیغه جدا کننده: این ابزارها برای جدا کردن یک قطعه کار از یک استوک بزرگتر استفاده می شوند. آنها یک خط جدایی تعریف شده با حداقل ضایعات ایجاد می کنند.
ابزار نخ زنی:
- ابزار برش نخ: برای ایجاد رزوه های خارجی روی قطعه کار طراحی شده است. آنها در اشکال و اندازه های مختلف برای نیازهای مختلف رزوه وجود دارند.
- ابزار تعقیب نخ: برای تعقیب یا بازیابی رشته های موجود استفاده می شود. این ابزار معمولا برای تعمیر نخ استفاده می شود.
ابزار شیارکاری:ابزار شیار کردن: این ابزارها شیارها یا فرورفتگی هایی روی قطعه کار ایجاد می کنند که اغلب برای قرار دادن حلقه های O، حلقه های نگهدارنده یا سایر ویژگی ها هستند.
ابزارهای مواجهه:ابزار مواجهه: برای ایجاد سطوح صاف در انتهای قطعه کار استفاده می شود. اغلب برای دستیابی به سطوح عمود بر هم یا حذف مواد از انتهای قطعه کار استفاده می شود.
ابزار جداسازی و شیاربندی:ابزار ترکیبی: این ابزار همه کاره برای هر دو عملیات جداسازی و شیار زدن طراحی شده اند و در زمان و تغییرات ابزار صرفه جویی می کنند.
ابزارهای نخ و شیار زنی:ابزار ترکیبی threading و Grooving: ایده آل برای کارهایی که نیاز به عملیات رزوه کاری و شیار زنی روی یک قطعه کار دارند.
ابزارهای پخ زدن:ابزار پخ زدن: برای ایجاد پخ یا لبه های اریب بر روی قطعه کار استفاده می شود. پخها اغلب برای بهبود ظاهر و سهولت مونتاژ قطعات ماشینکاری شده استفاده میشوند.
ابزارهای Knurling:ابزار Knurling: Knurling فرآیند ایجاد یک الگوی بافت روی یک قطعه کار است که معمولاً برای بهبود چسبندگی یا زیبایی شناسی است. ابزارهای خنجر در طرح ها و طرح های مختلفی وجود دارند.
ابزار شکل دهی:ابزار فرم: این ابزارها به صورت سفارشی برای هندسه قطعات خاص طراحی شده اند که اغلب برای تولید اشکال پیچیده و غیر استاندارد استفاده می شود.
ابزارهای تخصصی:ابزارهای پروفایل: برای ایجاد پروفایل های پیچیده روی قطعه کار استفاده می شود.
ابزارهای روکشی و چرخشی: اینها هم برای عملیات رو به رو و هم برای چرخش طراحی شده اند.
ابزارهای برش: برای برش قطعه کار برای ایجاد قطعات جداگانه یا حذف مواد اضافی طراحی شده است.
انتخاب ابزار برش مناسب به عواملی مانند ماده در حال ماشینکاری، پرداخت مورد نظر، ابعاد مورد نیاز و عملیات خاص بستگی دارد. برای اطمینان از ماشینکاری کارآمد و دقیق، انتخاب ابزار مناسب و نگهداری صحیح از آن ضروری است. انتخاب ابزار مناسب، همراه با راه اندازی و تنظیم صحیح، برای دستیابی به نتایج با کیفیت بالا در عملیات تراش بسیار مهم است.
اجزای یک ابزار برش تراش
ابزار برش تراش ابزار دقیقی است که برای شکل دادن، برش و حذف مواد از قطعه کار طراحی شده است. برای درک نحوه عملکرد و نحوه تنظیم صحیح آن، آشنایی با اجزای مختلف آن بسیار مهم است. در اینجا اجزای اصلی ابزار برش تراش آورده شده است:
- نگهدارنده ابزار:نگهدارنده ابزار قسمتی است که ابزار برش را در جای خود محکم می کند. به پست ابزار ماشین تراش متصل می شود و استحکام و پایداری لازم را برای عملیات ماشینکاری فراهم می کند. نگهدارنده های ابزار در طرح های مختلفی برای قرار دادن انواع ابزارهای برش وجود دارند.
- ساقه:ساقه قسمتی از ابزار برش است که در جا ابزار قرار می گیرد. معمولاً استوانه ای است و به طور ایمن در نگهدارنده بسته می شود. ابعاد و شکل ساقه ممکن است بر اساس نوع ابزار و طراحی متفاوت باشد.
- لبه برش:لبه برش قسمت تیز ابزار است که با قطعه کار تماس می گیرد و مواد را از آن جدا می کند. کیفیت لبه برش و هندسه آن به طور قابل توجهی بر عملکرد برش و پرداخت سطح تأثیر می گذارد. حفظ وضوح و دقت لبه برش ضروری است.
- قرار دادن:بسیاری از ابزارهای برش مدرن از درج های قابل تعویض استفاده می کنند که معمولاً از مواد سخت مانند کاربید یا سرامیک ساخته می شوند. این درج ها دارای هندسه برش هستند و در یک جیب روی ابزار برش محکم می شوند. آنها را می توان در صورت فرسوده شدن یا آسیب دیدگی چرخانده یا تعویض کرد و عمر ابزار را طولانی تر کرد.
- بینی ابزار:دماغه ابزار همان نوک ابزار برش است که در آن لبه برش و درج (در صورت استفاده) به هم می رسند. دماغه ابزار باید به طور دقیق قرار گرفته و برای ماشینکاری دقیق تراز باشد. برخی از ابزارهای برش تراش دارای شعاع دماغه ابزار قابل تنظیم برای کنترل بهتر بر عملکرد ابزار هستند.
- کنار ابزار:لبه ابزار سطح جانبی ابزار برش است که بخشی از لبه برش نیست. زوایای فاصله مناسب در کناره ابزار، تخلیه تراشه را تضمین می کند و اصطکاک بین ابزار و قطعه کار را کاهش می دهد.
- Tool Rake Face:صفحه چنگک سطحی از ابزار برش است که رو به قطعه کار است. زاویه و وضعیت صفحه چنگک بر شکل گیری تراشه و کارایی فرآیند برش تأثیر می گذارد. زاویه چنگک یک جنبه مهم از هندسه ابزار است.
- زاویه تسکین ابزار:زاویه تسکین زاویه بین جنب ابزار و محور ابزار است. این تضمین می کند که لبه برش به قطعه کار ساییده نمی شود و اصطکاک و تولید گرما را کاهش می دهد.
- زاویه پاکسازی ابزار:زاویه فاصله، زاویه بین سطح چنگک و سطح قطعه کار است. این اجازه می دهد تا تراشه ها به آرامی جریان داشته باشند و از تداخل بین ابزار و قطعه کار جلوگیری می کند.
- چیپ شکن (در صورت وجود):برخی از ابزارهای برش، به ویژه آنهایی که برای عملیات خشن استفاده می شوند، دارای یک تراشه شکن، یک شیار یا بریدگی روی صفحه چنگک هستند. تراشه شکن به کنترل تشکیل تراشه و بهبود تخلیه تراشه کمک می کند.
مونتاژ، تراز و نگهداری مناسب این اجزا برای دستیابی به ماشینکاری دقیق و کارآمد ضروری است. انتخاب ابزار برش و تنظیم آن باید متناسب با عملیات ماشینکاری خاص و موادی باشد که روی آن کار می شود. بازرسی و نگهداری منظم اجزای ابزار برش نیز برای اطمینان از نتایج ثابت و با کیفیت ضروری است.
انتخاب ابزار برش مناسب برای کار
انتخاب ابزار برش مناسب یک تصمیم حیاتی در هر عملیات ماشینکاری است، زیرا بر کیفیت، کارایی و دقت کار تاثیر زیادی دارد. هنگام انتخاب ابزار برش مناسب برای یک کار خاص باید چندین فاکتور را در نظر گرفت. در اینجا راهنمای نحوه انتخاب ابزار برش مناسب برای پروژه ماشینکاری شما آمده است:
1. مواد قطعه کار:
ماده ای که ماشینکاری می کنید یکی از مهم ترین عوامل در انتخاب ابزار است. مواد مختلف سختی، رسانایی حرارتی و سایندگی متفاوتی دارند. موارد زیر را در نظر بگیرید:
- سختی: مواد سخت مانند فولاد سخت شده یا سرامیک ها برای مقاومت در برابر نیروهای برش بالا به ابزارهای برشی با لبه های برش سخت مانند درج های کاربید نیاز دارند.
- مواد نرم: برای مواد نرم تر مانند آلومینیوم یا پلاستیک، فولاد پرسرعت (HSS) یا سایر مواد ابزار ممکن است کافی باشد.
2. عملیات ماشینکاری:
عملیات خاصی که انجام می دهید، مانند تراشکاری، فرز، سوراخ کاری، رزوه کشی، یا شیار زدن، نوع ابزار برش مورد نیاز شما را تعیین می کند. ابزارهای مختلفی برای کارهای مختلف طراحی شده اند و انتخاب مناسب عملکرد مطلوب را تضمین می کند.
3. سرعت برش و نرخ تغذیه:
سرعت برش و نرخ تغذیه مورد نیاز را بر اساس مواد و عملیات ماشینکاری تعیین کنید. سازندگان ابزار برش توصیه هایی را برای این پارامترها بر اساس طراحی ابزار و مواد در حال ماشینکاری ارائه می دهند. رعایت این توصیه ها برای دستیابی به نتایج مطلوب بسیار مهم است.
4. هندسه ابزار:
هندسه ابزار برش شامل زاویه چنگک، زاویه فاصله و شعاع دماغه ابزار را در نظر بگیرید. هندسه ابزار باید با مواد و نوع برش مطابقت داشته باشد. به عنوان مثال، زاویه چنگک زدن مثبت برای مواد نرم تر مناسب است، در حالی که زاویه چنگک منفی برای مواد سخت تر بهتر است.
5. ابعاد قطعه کار:
اندازه و ابعاد قطعه کار نیز بر انتخاب ابزار تأثیر می گذارد. برخی از ابزارهای برش برای عملیات زبر برای حذف سریع مواد حجیم مناسب تر هستند، در حالی که برخی دیگر برای تکمیل برای دستیابی به ابعاد دقیق و پرداخت سطح طراحی شده اند.
6. الزامات تکمیل سطح:
اگر به سطح خاصی نیاز دارید، ابزار برشی با هندسه و وضوح مناسب انتخاب کنید. ابزارهای تکمیل برای ارائه سطح صاف تری طراحی شده اند، در حالی که ابزارهای زبر برای حذف مواد کارآمدتر هستند.
7. مواد ابزار:
انتخاب مواد ابزار بسیار مهم است. ابزارهای کاربید، فولاد پرسرعت (HSS)، سرامیک و ابزارهای روکش دار همگی مزایا و محدودیت های خود را دارند. عواملی مانند عمر ابزار، مقاومت در برابر سایش و هزینه مواد ابزار را در تصمیم خود در نظر بگیرید.
8. خنک کننده و روانکاری:
در نظر بگیرید که آیا عملیات برش به مایع خنک کننده یا روانکاری نیاز دارد. برخی از مواد در حین ماشینکاری گرمای بیش از حد تولید می کنند و استفاده از خنک کننده یا روان کننده مناسب می تواند عمر ابزار را افزایش داده و عملکرد برش را بهبود بخشد.
9. پوشش ابزار:
بسیاری از ابزارهای برش مدرن با پوشش های تخصصی مانند TiN (نیترید تیتانیوم) یا TiAlN (نیترید آلومینیوم تیتانیوم) برای بهبود مقاومت در برابر سایش و کاهش اصطکاک عرضه می شوند. ابزاری با پوشش مناسب برای کاربرد خاص خود انتخاب کنید.
10. ملاحظات هزینه:
متعادل کردن هزینه ابزار برش با عملکرد و طول عمر آن بسیار مهم است. در حالی که ابزارهای ممتاز ممکن است عمر ابزار طولانیتر و عملکرد بهتری را ارائه دهند، یافتن تعادلی که با بودجه پروژه شما هماهنگ باشد ضروری است.
11. سازگاری نگهدارنده ابزار و ماشین:
اطمینان حاصل کنید که ابزار برش انتخابی با سیستم نگهدارنده ابزار تراش یا مرکز ماشینکاری شما سازگار است. نگهدارنده ابزار باید ثبات و استحکام ابزار برش را در طول فرآیند ماشینکاری فراهم کند.
در نهایت، ابزار برش مناسب برای کار به ترکیبی از این عوامل بستگی دارد. همیشه با توصیههای سازنده ابزار مشورت کنید و اگر مطمئن نیستید از ماشینکارهای با تجربه یا کارشناسان ابزارآلات مشاوره بگیرید. انتخاب و راه اندازی مناسب ابزار برای دستیابی به نتایج ماشینکاری کارآمد و دقیق ضروری است.
راه اندازی ابزار برش تراش
راه اندازی ابزار برش تراش برای تراشکاری CNC یک فرآیند سیستماتیک است که شامل چندین مرحله حیاتی است. هر مرحله برای اطمینان از اینکه ابزار برش به درستی در موقعیت و تراز قرار گرفته است، حیاتی است و در نهایت منجر به ماشینکاری دقیق و کارآمد می شود. بیایید مراحل را مرحله به مرحله طی کنیم:
مرحله 1: آماده سازی دستگاه تراش و قطعه کار
قبل از اینکه بتوانید ابزار برش را راه اندازی کنید، ضروری است که هم تراش و هم قطعه کار را آماده کنید:
- قطعه کار را ایمن کنید: مطمئن شوید که قطعه کار به طور ایمن در چاک تراش یا کلت بسته شده است. اطمینان حاصل کنید که بدون هیچ گونه لرزش یا لرزش به آرامی می چرخد.
- ایمنی: اطمینان حاصل کنید که تمام اقدامات ایمنی، از جمله استفاده از تجهیزات حفاظت فردی مناسب (PPE) و تنظیمات صحیح تراش وجود دارد.
مرحله 2: انتخاب نگهدارنده ابزار صحیح
نگهدارنده ابزار یک جزء حیاتی در فرآیند راه اندازی است. نگهدارنده ابزار مناسب را بر اساس عواملی مانند نوع ابزار برش، عملیات انجام شده و سیستم پست ابزار تراش انتخاب کنید.
- نگهدارنده ابزار را با ابزار برش مطابقت دهید: اطمینان حاصل کنید که نگهدارنده ابزار با نوع و اندازه ابزار برشی که قصد استفاده از آن را دارید، سازگار است.
- استحکام نگهدارنده ابزار: نگهدارنده ابزاری را انتخاب کنید که ثبات و استحکام را فراهم کند. این امر به ویژه در کاربردهای با دقت بالا بسیار مهم است.
مرحله 3: نصب ابزار برش
نصب ابزار برش شامل محکم کردن آن در نگهدارنده ابزار و اطمینان از قرار گرفتن محکم و صحیح آن است:
- ابزار برش را ایمن کنید: ابزار برش را داخل نگهدارنده ابزار قرار دهید و مکانیزم های گیره مانند پیچ های تنظیم یا کلت ها را سفت کنید. مطمئن شوید که ابزار به طور ایمن نگه داشته شده است.
- گرایش: بررسی کنید که جهت گیری ابزار برش نسبت به قطعه کار درست باشد. ابزار باید طوری قرار گیرد که قطعه کار را در زاویه و عمق مورد نظر درگیر کند.
مرحله 4: تنظیم ارتفاع ابزار و تراز خط مرکزی
ارتفاع ابزار و تراز خط مرکزی صحیح برای دستیابی به ابعاد ماشینکاری دقیق بسیار مهم است:
- تنظیم ارتفاع ابزار: ارتفاع ابزار را طوری تنظیم کنید که آن را با خط مرکزی دوک تراش تراز کند. از ارتفاع سنج ابزار یا نوار تست برای تنظیم ارتفاع مناسب ابزار استفاده کنید.
- تراز خط مرکزی: اطمینان حاصل کنید که ابزار با خط مرکزی دوک تراش هم تراز است. ناهماهنگی می تواند منجر به ماشینکاری خارج از مرکز شود که بر دقت قطعه تأثیر می گذارد.
مرحله 5: تنظیم جبران شعاع بینی ابزار
برای تراشکاری CNC، جبران شعاع دماغه ابزار، هندسه ابزار برش را به حساب می آورد. این امر به ویژه هنگام استفاده از ابزارهای درج مهم است:
- شعاع بینی ابزار را تعیین کنید: شعاع بینی دقیق درج ابزار برشی که استفاده می کنید را اندازه گیری یا جستجو کنید.
- مقدار Radius را وارد کنید: در نرم افزار کنترل CNC، مقدار شعاع دماغه ابزار اندازه گیری شده را وارد کنید تا مطمئن شوید که دستگاه در هنگام ماشینکاری، هندسه ابزار را جبران می کند.
مرحله 6: تنظیم افست های ابزار
آفست ابزار تغییرات در ابعاد ابزار و هندسه قطعه کار را شامل می شود. آنها اطمینان می دهند که موقعیت ابزار به طور دقیق برای ماشینکاری تنظیم شده است:
- افست ابزار صحیح را انتخاب کنید: مقدار افست ابزار مناسب را بر اساس هندسه ابزار و عملیات ماشینکاری تعیین کنید. این مقدار افست هر گونه اختلاف را جبران می کند.
- مقادیر افست را وارد کنید: مقادیر افست انتخابی را در نرم افزار کنترل CNC وارد کنید. این مقادیر به دستگاه نحوه تنظیم دقیق موقعیت ابزار را آموزش می دهد.
در طول فرآیند راه اندازی ابزار، از ابزارهای اندازه گیری دقیق مانند میکرومترها، ارتفاع سنج ها و نشانگرهای شماره گیری برای تأیید و تنظیم دقیق تراز ابزار استفاده کنید. ابزار برش را به طور مرتب بازرسی و نگهداری کنید تا مطمئن شوید که تیز و در شرایط خوب باقی می ماند، زیرا ابزاری که به خوبی نگهداری می شود به نتایج ماشینکاری ثابت و دقیق کمک می کند.
راه اندازی صحیح ابزار برش تراش در این مراحل برای دستیابی به نتایج بهینه در عملیات تراشکاری CNC بسیار مهم است. دقت و توجه به جزئیات در هنگام راه اندازی ابزار از عوامل کلیدی در تولید قطعات ماشینکاری شده با کیفیت بالا است.
بهینه سازی پارامترهای برش برای تراشکاری CNC
بهینه سازی پارامترهای برش برای دستیابی به عملیات تراشکاری CNC کارآمد و با کیفیت ضروری است. چهار جنبه کلیدی که هنگام بهینه سازی پارامترهای برش باید در نظر گرفته شود عبارتند از: سرعت و تغذیه، عمق برش، مایعات برش و روان کننده ها و مدیریت عمر ابزار.
1. سرعت ها و فیدها:
- آ. سرعت برش (سرعت سطح):سرعت برش که اغلب به عنوان سرعت سطحی نامیده می شود، سرعتی است که قطعه کار و ابزار برش در آن برهم کنش دارند. این بر حسب فوت سطح در دقیقه (SFM) یا متر در دقیقه (m/min) اندازه گیری می شود. برای بهینه سازی سرعت برش، مواد در حال ماشین کاری و مواد ابزار را در نظر بگیرید. برای مثال، ابزارهای فولادی با سرعت بالا (HSS) سرعت برش توصیه شده کمتری نسبت به ابزارهای کاربید دارند. برای تعیین سرعت برش توصیه شده برای مواد و ابزار خاص، با اطلاعات سازنده ابزار یا کتابچه های راهنمای ماشینکاری مشورت کنید.
- ب نرخ خوراک:نرخ تغذیه سرعت خطی است که ابزار برش به داخل قطعه کار پیش می رود. این بر حسب اینچ در هر دور (IPR) یا میلیمتر در هر دور (mm/rev) اندازهگیری میشود. برای بهینهسازی نرخ تغذیه، عواملی مانند خواص مواد، هندسه ابزار و سطح مورد نظر را در نظر بگیرید. نرخهای تغذیه بالاتر معمولاً مولدتر هستند، اما ممکن است به ابزارهای محکمتری نیاز داشته باشند.
- ج رابطه سرعت برش و نرخ خوراک:متعادل کردن سرعت برش و نرخ تغذیه برای حذف کارآمد مواد بسیار مهم است. افزایش سرعت برش به طور معمول اجازه می دهد تا نرخ تغذیه بالاتری داشته باشد، اما این دو باید با هم تنظیم شوند تا از سایش ابزار و گرمای بیش از حد جلوگیری شود.
2. عمق برش:
- آ. عمق برش (DOC):عمق برش فاصله ای است که ابزار برش به قطعه کار نفوذ می کند. در نظر گرفتن قابلیت های مواد و ابزار ضروری است. عمق برش را بر اساس سختی مواد و استحکام و استحکام ابزار بهینه کنید. برش های کم عمق ممکن است برای مواد سخت تر لازم باشد، در حالی که برش های عمیق تر را می توان در مواد نرم تر به دست آورد.
- ب عمق برش محوری و شعاعی:در تراشکاری CNC، عمق برش محوری (در امتداد طول قطعه کار) و شعاعی (در سراسر قطر قطعه کار) را در نظر بگیرید. عمق بهینه برای هر کدام بر اساس عملیات و مواد متفاوت خواهد بود.
3. برش مایعات و روان کننده ها:
- آ. انتخاب مایع برش مناسب:سیالات برش برای دفع گرما، کاهش اصطکاک و بهبود تخلیه تراشه ضروری هستند. سیال برش مناسب را بر اساس مواد و عملیات ماشینکاری انتخاب کنید. خنک کننده های محلول در آب، خنک کننده های مبتنی بر روغن معدنی یا مصنوعی ممکن است برای مواد مختلف ترجیح داده شوند.
- ب کاربرد مناسب:مایعات برش را به طور موثر در ناحیه برش بمالید تا از روانکاری و خنک سازی کافی اطمینان حاصل کنید. این کار را می توان از طریق خنک کننده سیل، سیستم های مه پاش، یا تحویل مایع خنک کننده از طریق ابزار، بسته به قابلیت های دستگاه انجام داد.
- ج نظارت و نگهداری:به طور مرتب سطوح، شرایط و آلودگی مایع برش را کنترل کنید تا مطمئن شوید که آنها مؤثر هستند. سیستم های مایع برش را برای جلوگیری از مسائلی مانند رشد و تخریب باکتری ها حفظ کنید.
4. مدیریت زندگی ابزار:
- آ. بازرسی و نگهداری ابزار:برای اطمینان از اینکه ابزارها در شرایط خوبی هستند، یک برنامه معمول بازرسی و نگهداری ابزار را اجرا کنید. ابزارهای کسل کننده یا آسیب دیده می توانند منجر به کیفیت پایین ماشینکاری و کاهش عمر ابزار شوند.
- ب برنامه تعویض ابزار:بر اساس عواملی مانند فرسودگی ابزار، زمان کارکرد دستگاه و الزامات تولید، برنامه تعویض ابزار تنظیم کنید. این به جلوگیری از خرابی غیرمنتظره ابزار و حفظ کیفیت ماشینکاری ثابت کمک می کند.
- ج بهینه سازی عمر ابزار:برخی از مواد و پوششهای ابزار عمر ابزار طولانیتری دارند. استفاده از ابزار با کارایی بالا را برای بهینه سازی عمر ابزار و کاهش زمان توقف تولید در نظر بگیرید.
- د کنترل تراشه ابزار:کنترل موثر تراشه، از جمله استفاده از تراشه شکن ها و هندسه مناسب ابزار، می تواند عمر ابزار را با کاهش سایش ناشی از تراشه افزایش دهد.
بهینه سازی پارامترهای برش در تراشکاری CNC یک فرآیند مداوم است. ممکن است برای یافتن بهترین پارامترها برای یک برنامه خاص به آزمایش و تنظیم دقیق نیاز باشد. به طور منظم این پارامترها را کنترل و تنظیم کنید تا از عملکرد بهینه ماشینکاری، عمر ابزار و کیفیت قطعه اطمینان حاصل کنید. پارامترهای برش بهینه سازی مناسب نه تنها کارایی ماشین کاری را بهبود می بخشد، بلکه سایش ابزار و در نهایت هزینه های تولید را کاهش می دهد.
عیب یابی مشکلات رایج در تنظیمات ابزار
عیب یابی مشکلات رایج در تنظیم ابزار یک مهارت ضروری برای ماشین آلات و اپراتورهای CNC است. درک و پرداختن به این مسائل می تواند به حفظ دقت و کیفیت عملیات ماشینکاری کمک کند. در اینجا برخی از مشکلات رایج تنظیم ابزار و راه حل های آنها آورده شده است:
1. چتر ابزار:
موضوع: صدای ابزار زمانی رخ میدهد که ابزار برش در طول فرآیند ماشینکاری ارتعاش میکند و منجر به پایان ضعیف سطح، سایش ابزار و آسیب احتمالی قطعه کار میشود.
راه حل:
- کاهش سرعت یا افزایش خوراک: پارامترهای برش را با کاهش سرعت برش یا افزایش نرخ تغذیه تنظیم کنید. این تغییر می تواند ارتعاشات را کاهش دهد و پچ پچ را کاهش دهد.
- بررسی صلبیت ابزار: اطمینان حاصل کنید که نگهدارنده ابزار و ابزار به درستی محکم شده اند و ابزار خیلی دور از نگهدارنده قرار نگرفته است.
- بستن قطعه کار را بررسی کنید: مطمئن شوید که قطعه کار محکم بسته شده است تا از هرگونه لرزش مربوط به قطعه کار جلوگیری شود.
- از تکنیک های مرطوب کننده استفاده کنید: برخی از ماشین ها دارای ویژگی هایی برای میرایی ارتعاشات هستند. در صورت وجود، استفاده از آنها را در نظر بگیرید.
- یک ابزار سفت تر را انتخاب کنید: یک ابزار سفت تر، مانند ابزاری با فلوت کمتر، می تواند به کاهش پچ پچ کمک کند.
2. پایان ضعیف سطح:
موضوع: پرداخت ضعیف سطح می تواند ناشی از مشکلات مربوط به تنظیم ابزار یا پارامترهای برش باشد که منجر به ایجاد سطوح ناهموار یا ناهمگون روی قطعه کار شود.
راه حل:
- بررسی هندسه ابزار: مطمئن شوید که هندسه ابزار برش برای عملیات مناسب است. یک ابزار تیز با هندسه صحیح برای دستیابی به یک سطح خوب بسیار مهم است.
- بهینه سازی پارامترهای برش: سرعت برش، نرخ تغذیه و عمق برش را تنظیم کنید تا بهترین ترکیب را برای مواد و عملیات خاص پیدا کنید.
- سایش ابزار را بررسی کنید: ابزار را برای علائم سایش یا آسیب، مانند لبه های بریده شده، بررسی کنید. در صورت نیاز، ابزار را جایگزین یا دوباره آسیاب کنید.
- از مایع برش مناسب استفاده کنید: روانکاری و خنک کاری مناسب می تواند به طور قابل توجهی بر روی سطح تأثیر بگذارد. از مایع برش مناسب برای مواد و عملیات استفاده کنید.
- به حداقل رساندن لرزش: برای جلوگیری از ایجاد بی نظمی سطح، مشکلات ارتعاش را برطرف کنید.
3. عدم دقت ابعاد:
موضوع: قطعات ممکن است به دلیل نامرتب بودن ابزار یا سایش ابزار، ابعاد نادرستی داشته باشند.
راه حل:
- تنظیمات ابزار را بررسی کنید: بررسی کنید که ابزار به درستی با ارتفاع و تراز مناسب نسبت به قطعه کار تنظیم شده باشد.
- ماشین کالیبره کردن: اطمینان حاصل کنید که دستگاه CNC به درستی کالیبره شده است و به طور دقیق افست های ابزار و داده های ابزار را تفسیر می کند.
- تنظیم افست ابزار: با اندازه گیری دقیق ابزار و وارد کردن مقادیر آفست مناسب در کنترل CNC، هرگونه خطا در افست ابزار را تصحیح کنید.
- سایش ابزار را بررسی کنید: ابزار برش را به طور مرتب از نظر سایش بررسی کنید و در صورت لزوم آن را تعویض یا دوباره آسیاب کنید.
4. مشکلات کنترل تراشه:
موضوع: کنترل نادرست تراشه می تواند منجر به مشکلاتی مانند گرفتگی تراشه، تخلیه ضعیف تراشه و آسیب به قطعه کار یا ابزار شود.
راه حل:
- هندسه ابزار مناسب را انتخاب کنید: یک ابزار برش با تراشه شکن یا هندسه مناسب برای مواد و عملکرد انتخاب کنید.
- بهینه سازی پارامترهای برش: نرخ تغذیه، سرعت برش و عمق برش را برای بهینه سازی شکل گیری و تخلیه تراشه تنظیم کنید.
- از روغن کاری مناسب استفاده کنید: استفاده صحیح از مایعات برش می تواند به روانکاری و تسهیل تخلیه تراشه کمک کند.
- بررسی تراز ابزار و قطعه کار: اطمینان حاصل کنید که ابزار به درستی با قطعه کار تراز شده است تا از مشکلات مربوط به تراشه جلوگیری شود.
5. شکستن ابزار:
موضوع: شکستن ابزار ممکن است به دلیل نیروی بیش از حد، تنظیم نادرست ابزار، یا مسائل مربوط به مواد رخ دهد.
راه حل:
- بهینه سازی پارامترهای برش: با تنظیم پارامترهایی مانند نرخ تغذیه، سرعت برش و عمق برش، نیروهای برش را کاهش دهید.
- تنظیمات ابزار را بررسی کنید: مطمئن شوید که ابزار به طور ایمن در نگهدارنده ابزار نصب شده است و به درستی تراز شده است.
- از مواد مناسب ابزار استفاده کنید: مواد ابزار مناسب را برای مواد خاصی که در حال ماشینکاری هستید انتخاب کنید. به عنوان مثال، ابزار کاربید برای مواد سخت بهتر است.
- بررسی سایش ابزار: به طور مرتب ابزار را از نظر علائم سایش بررسی کنید و قبل از اینکه بیش از حد فرسوده شود و مستعد شکستگی شود، آن را تعویض کنید.
پرداختن به این مسائل رایج تنظیم ابزار نیاز به ترکیبی از آموزش مناسب، تعمیر و نگهداری منظم و یک رویکرد سیستماتیک برای عیب یابی دارد. توانایی تشخیص و حل مشکلات مربوط به ابزار برای دستیابی به نتایج ماشینکاری با کیفیت بالا و کارآمد بسیار مهم است.
در نتیجه
فرآیند راه اندازی و بهینه سازی ابزارهای برش تراش برای تراشکاری CNC یکی از جنبه های مهم ماشین کاری است که به طور قابل توجهی بر کیفیت، کارایی و دقت فرآیندهای تولید تأثیر می گذارد. درک عمیق اجزاء و عملکرد ابزارهای برش و همچنین عوامل دخیل در انتخاب ابزار برای ماشین آلات و اپراتورهای CNC ضروری است.
راه اندازی صحیح یک ابزار برش شامل یک رویکرد سیستماتیک است، از آماده سازی ماشین تراش و قطعه کار گرفته تا انتخاب نگهدارنده ابزار مناسب، نصب ابزار، تنظیم ارتفاع ابزار و تراز خط مرکزی، و پیکربندی جبران شعاع دماغه ابزار و جابجایی ابزار. هر مرحله نقشی اساسی در دستیابی به نتایج ماشینکاری دقیق و کارآمد دارد.
بهینه سازی پارامترهای برش، از جمله سرعت و تغذیه، عمق برش، سیالات برش، و مدیریت عمر ابزار، یکی دیگر از جنبه های مهم تراشکاری CNC است. با انتخاب دقیق پارامترهای مناسب، ماشینکاران میتوانند بهرهوری را افزایش دهند، طول عمر ابزار را حفظ کنند و کیفیت پرداخت سطح را بهبود بخشند.
در نهایت، توانایی عیب یابی مشکلات رایج تنظیم ابزار، مانند صدای زنگ ابزار، سطح ضعیف، عدم دقت ابعاد، مشکلات کنترل تراشه، و شکستگی ابزار، برای حفظ نتایج ماشینکاری ثابت و با کیفیت بالا ضروری است. شناسایی این مسائل و اجرای راه حل های مناسب تضمین می کند که فرآیند ماشینکاری صاف و کارآمد باقی می ماند.
به طور کلی، درک جامع ابزارهای برش تراش و راه اندازی آنها، همراه با توانایی بهینه سازی پارامترهای برش و عیب یابی مشکلات، ماشینکاران را قادر می سازد تا به بهترین نتایج در عملیات تراشکاری CNC دست یابند. یادگیری، آموزش و تجربه مستمر در اصلاح این مهارتها و تضمین موفقیتآمیز فرآیندهای ماشینکاری کلیدی هستند.
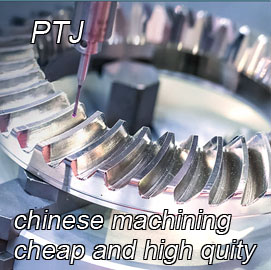
- ماشینکاری 5 محور
- تراش تراش
- چرخش CNC
- صنایع ماشینکاری
- فرآیند ماشینکاری
- درمان سطحی
- ماشینکاری فلز
- ماشینکاری پلاستیک
- قالب متالورژی پودر
- قالب ریخته گری
- گالری قطعات
- قطعات فلزی خودرو
- قطعات ماشین آلات
- LED هیت سینک
- قطعات ساختمان
- قطعات موبایل
- قطعات پزشکی
- قطعات الکترونیکی
- ماشینکاری خیاطی
- قطعات دوچرخه
- ماشینکاری آلومینیوم
- ماشینکاری تیتانیوم
- ماشینکاری فولاد ضد زنگ
- ماشینکاری مس
- ماشینکاری برنجی
- ماشینکاری فوق آلیاژی
- ماشین کاری پیک
- ماشینکاری UHMW
- ماشینکاری یک طرفه
- ماشینکاری PA6
- ماشینکاری PPS
- ماشینکاری تفلون
- ماشینکاری اینکونل
- ماشینکاری فولاد ابزار
- مواد بیشتر